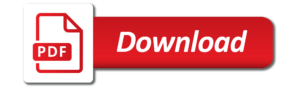
Airflow Range: 500~56,000 m³/h (294~32,941CFM)
Static Pressure Range: 136~1,400 Pa (0.55~5.62 in.WG.)
Drive Type: Belt/ Direct drive
Mounting Types: Base Mount/ Ceiling Hung
Applications: Industrial ventilation / Explosion proof air exhaust / Kitchen fume exhaust
The scroll is fixed by 8 equally spaced bolts. Discharge directions can be adjusted at the jobsite within the allowable angle range.
The fan shall be tested and certified in accordance with AMCA Standard 210 & 300,UL 705. AMCA Seal for (Efficiency Sound, Air Performance and Fan energy index) shall be tagged on each fan before leaving the factory as a standard seal, for other seals shall be tagged on the fan according to application and customer needs.
The manufacturer shall obtain Production License for National Industrial Products and be certified by ISO 9001, ISO 14001, ISO 45001.
The fan shall be direct or belt drive type, with an aluminum backward inclined centrifugal wheel. The inlet cone shall
have a curved section to ensure smooth air movement. Each wheel shall be statically and dynamically balanced up to
grade G 2.5 as per ISO 1940.
The fan housing shall be constructed of steel. It shall be thick and strong enough to support the drive mechanism and motor. The scroll shall be continuously welded. The fan surface shall go through the processes of alkaline wash and Parkerizing and be finished with electrostatic epoxy coatings in black or other colors specified by customers.
Both the wheel and inlet shall be constructed of aluminum. Access door: An access door must be provided for the scroll to remove possible foreign bodies inside of the fan. The platform on which the fan is placed shall be a stable and level one and vibration isolators shall be used for connection. The pre-embedded fixing method shall not be required.
Standard belt drive CUS fans that include a shaft/bearing guard and belt guard are for indoor installation.
For outdoor installation, there shall be a rain cover that offers total protection for the motor and other driving parts.
Fan Part |
Description |
Shaft |
The shaft shall be heat treated through homogenizing furnace to the hardness level of HB370, and the hard film shall be applied on the surface to avoid corrosion. The shaft shall also be subject to balancing tests together with the wheel. The design speed of the shaft shall be at least 25% more than the maximum running speed of the fan.
|
Bearings |
Metal bearings shall be used to support the fan shaft to avoid vibrations directly coming onto the motor. The bearing life shall be (80, 000 to 150,000) hours at the maximum operating speed specified in the catalog as per the design. The bearing shall be of permanently sealed type and metal pillow block ball bearing that can be lubricated.
|
Drive Support |
Drive mechanism shall be supported by heavy gauge steel sheet finished with powder coatings to avoid corrosion. The belt tension can be adjusted through the adjusting bolt at the motor base. The design shall make sure the fan shaft and motor shaft is always parallel.
|
Pulley |
Fan pulleys shall be sized for a minimum of 150% of the driving power. Pulleys shall be cast iron, keyed and securely attached to the wheel and motor shaft. Conical type bushings shall be equipped for easy removal of the pulley.
|
Motor |
The motor shall be carefully matched to the fan load. It shall be (IP55,IP56, …etc) rated with Class F,H Insulation according to project specification . The motor bearing shall be of ball type and lubrication- free. Out of the air stream shall the motor and drive mechanism be located to avoid grease or dirt accumulation.
|
Fan Part | Description |
Shaft |
The shaft shall be heat treated through homogenizing furnace to the hardness level of HB370, and the hard film shall be applied on the surface to avoid corrosion. The shaft shall also be subject to balancing tests together with the wheel. The design speed of the shaft shall be at least 25% more than the maximum running speed of the fan.
|
Bearings |
Metal bearings shall be used to support the fan shaft to avoid vibrations directly coming onto the motor. The bearing life shall be (80, 000 to 150,000) hours at the maximum operating speed specified in the catalog as per the design. The bearing shall be of permanently sealed type and metal pillow block ball bearing that can be lubricated.
|
Drive Support |
Drive mechanism shall be supported by heavy gauge steel sheet finished with powder coatings to avoid corrosion. The belt tension can be adjusted through the adjusting bolt at the motor base. The design shall make sure the fan shaft and motor shaft is always parallel.
|
Pulley |
Fan pulleys shall be sized for a minimum of 150% of the driving power. Pulleys shall be cast iron, keyed and securely attached to the wheel and motor shaft. Conical type bushings shall be equipped for easy removal of the pulley.
|
Motor |
The motor shall be carefully matched to the fan load. It shall be (IP55,IP56, …etc) rated with Class F,H Insulation according to project specification . The motor bearing shall be of ball type and lubrication- free. Out of the air stream shall the motor and drive mechanism be located to avoid grease or dirt accumulation.
|